IRT Analyzer APC
A powerful yet user-friendly software platform that lets industrial engineers and automation specialists harness the full potential of thermal imaging for process control. Designed for 24/7 reliability and seamless integration into industrial systems, it combines infrared image analysis with automation capabilities to monitor equipment and processes in real-time.

Key Features
IRT Analyzer APC comes packed with features that make thermal monitoring and automation easy and effective. Its clear, no-code interface allows engineers to set up complex monitoring logic without programming, while under the hood it offers advanced tools for deep analysis.

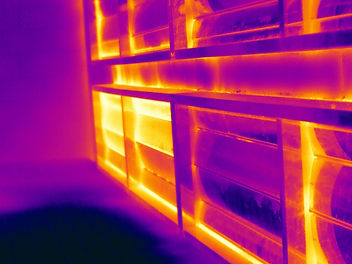
-
Multi-Camera Data Acquisition: Connect and collect data from multiple infrared cameras simultaneously for comprehensive coverage of your assets and processes. IRT Analyzer APC efficiently handles all incoming thermal data streams in real time.
-
Robust Analysis Tools: Leverage a full spectrum of thermographic analysis tools for detailed image evaluation and accurate diagnostics. Zoom into images, compare temperature profiles, and detect even the smallest thermal anomalies that could indicate a problem.
-
Intelligent Process Automation: Create automated process control logic with flexibility and precision. Define rules and conditions (without writing code) that trigger actions—such as adjusting a heater, sounding an alarm, or pausing a production line—based on thermal thresholds or trends.
-
Alarms & External I/O: Stay informed with responsive alarm notifications and integrate with external systems easily. IRT Analyzer APC supports digital I/O and standard industrial protocols, so it can send alerts or signals to PLCs, SCADA systems, or operators the moment temperatures stray out of spec.
-
Trend Analysis & Recording: Track temperature trends over time with built-in graphing and logging. The software records continuous data and provides statistical tools to help predict equipment behavior, enabling predictive maintenance and process optimizations. Historical data and trends can be reviewed to identify patterns or gradual changes that might be missed in live views.
-
Smart Camera Control: Optimize imaging quality with automatic camera shutter control and calibration features. IRT Analyzer APC can manage camera settings (like focus, shutter, and range) on the fly to ensure you always get clear, accurate thermal images even as conditions change.
-
Industrial Protocol Compatibility: Enjoy hassle-free integration into your existing operations – the platform speaks Modbus, OPC, Ethernet/IP and other common industrial languages out-of-the-box. This means the thermal monitoring system can directly communicate with factory automation equipment and third-party software, fitting right into your Industry 4.0 ecosystem.
-
Custom Scripting Extensibility: For special requirements, take advantage of Python script integration to extend functionality. Advanced users can implement custom analytics, decision algorithms, or connectivity options, tailoring the system to unique use cases beyond the standard feature set.

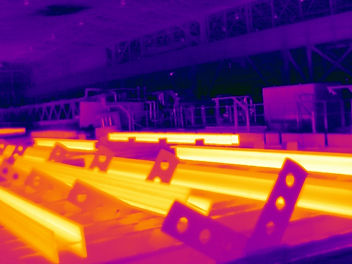
Industries We Serve – Real-World Applications
IRT Analyzer APC is trusted across diverse industries to ensure things run safely, smoothly, and efficiently. Wherever temperature is a key factor – either as a useful signal of equipment health or a parameter to control – this solution finds a home. Here are some of the most relevant industries and how they benefit from IRT Analyzer APC.
Manufacturing & Production
In automotive, electronics, plastics, food processing and more, thermal monitoring is vital for quality control and equipment maintenance. IRT Analyzer APC watches over production lines to verify that heat-dependent processes (like welding, soldering, molding or heat sealing) are within the right parameters. For example, packaging lines use it to check seal integrity and fill levels of products in real-time; any defective seal or abnormal temperature pattern triggers an immediate alert or rejects the item, ensuring 100% quality compliance. Additionally, critical machinery such as motors, conveyors, and ovens are continuously scanned for early signs of overheating or stress, allowing maintenance teams to fix issues before they cause unplanned downtime.


Heavy Industry (Metals, Glass, Cement)
In steel mills, foundries, and cement plants, operating conditions are extreme and the stakes are high. IRT Analyzer APC is widely used as a preventive maintenance and safety system for equipment like ladles, kilns, and furnaces. By analyzing the temperature distribution on a ladle’s exterior, for instance, the software can detect refractory lining failures or dangerous hot spots well before a breakout of molten metal occurs. This early warning allows operators to take action and prevent catastrophic accidents, protecting personnel and avoiding costly equipment damage. In cement production, similar thermal monitoring of rotary kilns helps maintain optimal temperatures and prevents overheating that could damage the kiln shell. These industries also use the recorded thermal data to optimize fuel usage and improve process efficiency, since even small temperature adjustments can lead to significant energy savings.


Energy & Utilities
Power generation plants (coal, gas, nuclear) and electrical utility companies rely on thermal imaging to continuously monitor transformers, switchgears, turbines, and other high-voltage equipment. IRT Analyzer APC integrates into substation monitoring systems to keep an eye on connections, breakers, and insulators – a spike in temperature can indicate electrical resistance or an impending failure. Early detection of an overheating transformer or cable means it can be fixed before causing a power outage or fire.
Similarly, in renewable energy installations like solar farms and wind turbines, thermal cameras controlled by IRT Analyzer APC help identify overheating components (e.g., solar panel hot spots or turbine gearboxes running hot) to schedule timely maintenance. The software’s alarm and protocol features can directly notify operators or even trigger automatic shutdown sequences for safety if a critical threshold is passed, ensuring maximum uptime and asset protection.
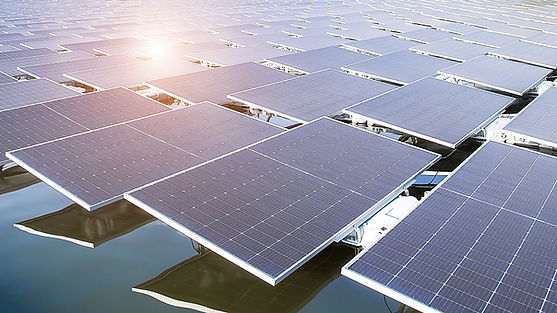

Chemical & Oil/Gas
In petrochemical plants, refineries, and battery energy storage facilities, early fire detection is paramount. IRT Analyzer APC is employed to monitor storage tanks, reactors, conveyor belts (e.g., coal or biomass handling), and other areas where a heat buildup could signal a fire risk. Thermal imaging can spot abnormal heating far sooner than traditional smoke alarms. For example, in chemical processing, a slight unexpected temperature rise in a vessel can warn of a reaction going out of control – the software will flag the deviation and can initiate emergency cooling or shutdown procedures immediately. In fuel storage or waste management sites, the system can scan for hot spots in real time, sending an alert at the first sign of a smoldering fire so that fire suppression systems or crews can respond before an explosion or fire outbreak. This predictive approach to safety saves money and lives, preventing disasters by catching them early.


Common Use Cases & Benefits
Across various industries, certain key use cases for IRT Analyzer APC stand out for their impact on productivity and safety.
Predictive Maintenance
Perhaps the most widespread use is catching issues before they become failures. By continuously monitoring equipment temperatures, the software helps maintenance teams address problems proactively. For instance, an abnormally warm bearing or electrical connection will show up in the thermal data long before it fails completely. IRT Analyzer APC can be set to recognize such trends and notify the team immediately. This predictive maintenance approach reduces unplanned downtime and extends the lifespan of machines, saving companies significant costs in repairs and lost production. It also improves safety by minimizing the risk of catastrophic failures (like a burned-out motor or electrical fire) through early intervention.
Quality Assurance & Process Optimization
In processes where temperature directly affects product quality (curing, baking, sealing, welding, etc.), IRT Analyzer APC ensures every item is made to spec. The system can automatically adjust process parameters – for example, increasing oven heat if a product is not reaching the target temperature, or slowing a conveyor if items need more cooling time – all based on live thermal feedback. Manufacturers use this to achieve uniform quality and reduce waste or rework. Moreover, by analyzing thermal profiles of the process over time, engineers can optimize cycle times and energy usage. Adding thermal cameras along a production line can monitor things like packaging seals, bottle fill levels, and drying processes, catching any deviation in real-time to avoid defective outputs.
Safety & Early Hazard Detection
Thermal anomaly detection is a cornerstone of facility safety now. IRT Analyzer APC excels at watching for the subtle signs of a developing hazard: a hotspot on a conveyor that could ignite material, a rise in a battery bank’s temperature that signals a thermal runaway, or an unseen smoldering fire inside a pile of raw material. The moment such a condition is detected, the system can trigger alarms, activate cooling or fire suppression systems, and guide operators to the exact location of the issue. In high-risk environments (mining conveyors, waste recycling plants, grain silos, etc.), this kind of automated thermal vigilance provides peace of mind that potential fires or overheating incidents won’t go unnoticed. Insurers and regulators increasingly appreciate these systems as part of comprehensive safety management.
Remote Monitoring & Control
For geographically distributed operations or hazardous areas, IRT Analyzer APC allows a hands-off, eyes-on approach. Engineers can supervise multiple sites from a central control room, or even securely over the web, since the software can stream thermal video and data to anywhere it’s needed. This is particularly useful in scenarios like offshore oil platforms, unmanned power substations, or sprawling factory floors – a few operators can oversee thermal data from all critical points without physically patrolling them. If an issue is spotted, they can often resolve it remotely by sending control commands (thanks to the software’s integration with control systems) or by guiding on-site personnel to the exact point of concern. The result is a more responsive and efficient operation, with less need for constant manual inspections. As the system is essentially always on guard, maintenance and operational staff can prioritize their efforts where it’s truly needed, improving overall productivity.
Documentation & Reporting
Beyond real-time action, IRT Analyzer APC automatically logs all measurements and events, building a rich dataset for analysis and compliance. Users can generate detailed reports with thermal images, trend graphs, and annotations at the click of a button. For industries with regulatory requirements or customer quality audits, this provides transparent evidence of process control and equipment condition over time. For example, a food manufacturer can produce thermal records of every batch’s pasteurization cycle to demonstrate safety compliance. Similarly, a facilities manager can maintain a maintenance log showing before-and-after thermal images of repaired equipment to validate that issues were resolved. Such documentation adds value by supporting continuous improvement initiatives and knowledge retention – tomorrow’s engineers can learn from the thermal history captured today.
Report Features
-
Report Generator for Microsoft Word
-
Pre-designed Templates
-
Template Customization and Custom Report Sections
-
IR Images, Visible Images, Diagrams, and Tables
-
Fields and Tables for All Relevant Data (Object Measurements, Metadata, etc.)
-
Document Properties
-
Table of Contents and Summary Tables
-
Formulas and Conditional Text
-
Formatting (Includes LUA-Based Expressions)
-
Title Pages, Extra Pages, and Section Management
-
Headers and Footers
-
Conditional Templates
-
Export Formats: PDF, XPS, ODT, and More
-
Extend Functionality with Macros (VBA Hooks)
Thermal Analysis Features
-
Multiple Color Palettes and Adjustable Temperature Range (Auto or Manual)
-
IR–Visible Fusion with Details
-
Enhancement and Alarm Range
Isotherms (Single or Interval) -
Emissivity & Environment Adjustments (Per Image or Per Analysis Object)
-
Analysis Objects: Spots, Lines, Areas (Rectangles, Circles, Ellipses, Polygons) with Min/Max/Average
-
Hot/Cold Spots Detection (Automatic Local Extremum)
-
Complex Lines and Polygons for More Detailed Analysis
-
Delta Analysis (Compare Objects or Subtract Reference Images)
-
Profiles (Line Profiles)
-
Histograms (Temperature Distribution)
-
Trends (Analysis Trends and Real-Time Trends)
-
Image Filters (Contrast Enhancement, Histogram and Plateau Equalization, Convolution Filters, etc.)
-
Multiple Image Analysis (Multi-Camera Live Composition, Image Subtraction, etc.)
Process Control Features
-
Automation Mode for Real-Time Image Analysis and Process Control
-
External IO: WAGO, National Instruments, Modbus TCP Server, Ethernet/IP, ...
-
Automation Logic: User-Defined Logical Operations on Measurements
-
Conditions & Triggers (Temp-Based, Analysis-Based, Time-Based, External Signals)
-
Alarms & Signals (On-Screen, External IO, Audio, etc.)
-
Measurement Outputs
-
Snapshots
-
Alarm Notification E-mails
-
Image Subtraction by a Trigger
-
Image Recorder with Triggers (Pre/Post Trigger Frames)
-
Trend Recorder with Triggers
-
Camera Shutter Control
-
Multi-Image Composition (Arrange Multiple Live Feeds Side-by-Side)
-
System Health Watchdog (Monitor Software/Hardware Status)
-
Multiple IRT Analyzer Instances in Parallel
-
Auto-Start / Auto-Load Projects on System Startup
-
Password Lock for Restricted Operation
System Requirements
IRT Analyzer has been designed to work with the following operation systems:
-
Microsoft Windows 10/11 or newer
-
x86/x64 (ARM is not supported)
Recommended Hardware
-
A quad-core processor with x64 architecture, 8 GB RAM (e.g. Intel N100 for 4x cameras 640x480@30fps)
-
Full HD (1920x1080) monitor resolution
Supported Thermal Cameras
-
FLIR, Fluke, Jenoptik, HikMicro, DIAS, NEC-Avio, Optris, Fotric